Business
- Home
- Business
時代は変わった。
必要な時に、
必要な分だけ。
在庫の圧縮や生産コストの最小化を目指す、ジャストインタイム
多様かつ急なニーズにも迅速に対応すべく、当社では「必要な時に、必要な分だけ」の生産方式を取り入れています。在庫リスクを減らして効率化し、生産現場のムダ・ムラ・ムリを徹底的になくして品質が良いものだけを製造。後工程に引き取られた分だけを生産・工程の流れ化・必要数に応じてラインタクトを決定することで、双方に大きなメリットを生み出します。
OEM/ODM
モノづくりに必要な全ての環境/設備が一拠点に
当社は「金属加工」「板金/組立」「ダイカスト金型」の3つの製造工場からなる製品化体制と、安定、一定した品質管理を供給する品質管理体制の全てを一拠点に集約。
ワンストップ対応だからこそ可能な付加価値あるモノづくりを提供します。
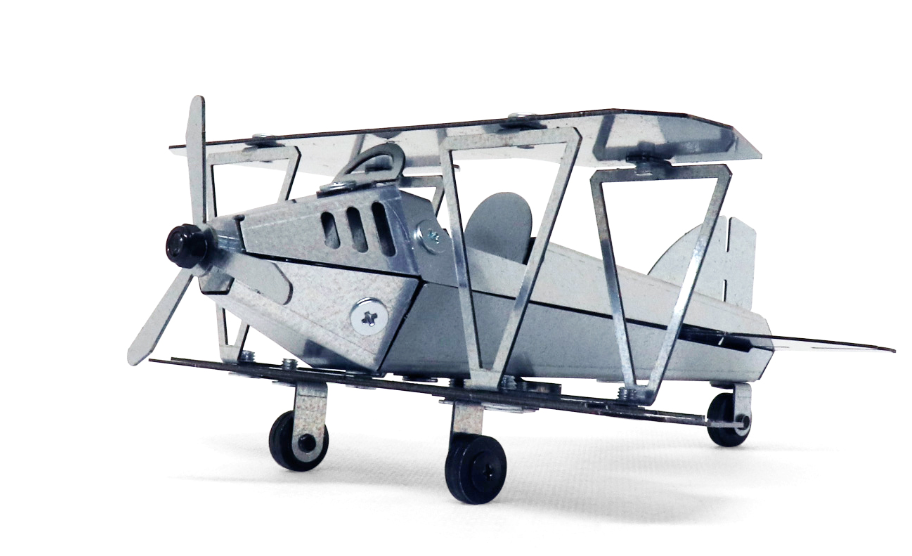
一拠点ワンストップ体制が生み出すお客様のメリット
利便性
- 窓口の一本化
- 管理コストの低減
品質管理
- 専門技術者が終結
- 技術/管理が一定
- 全行程を一元管理
カスタマイズ
- 迅速な対応
- 柔軟な対応
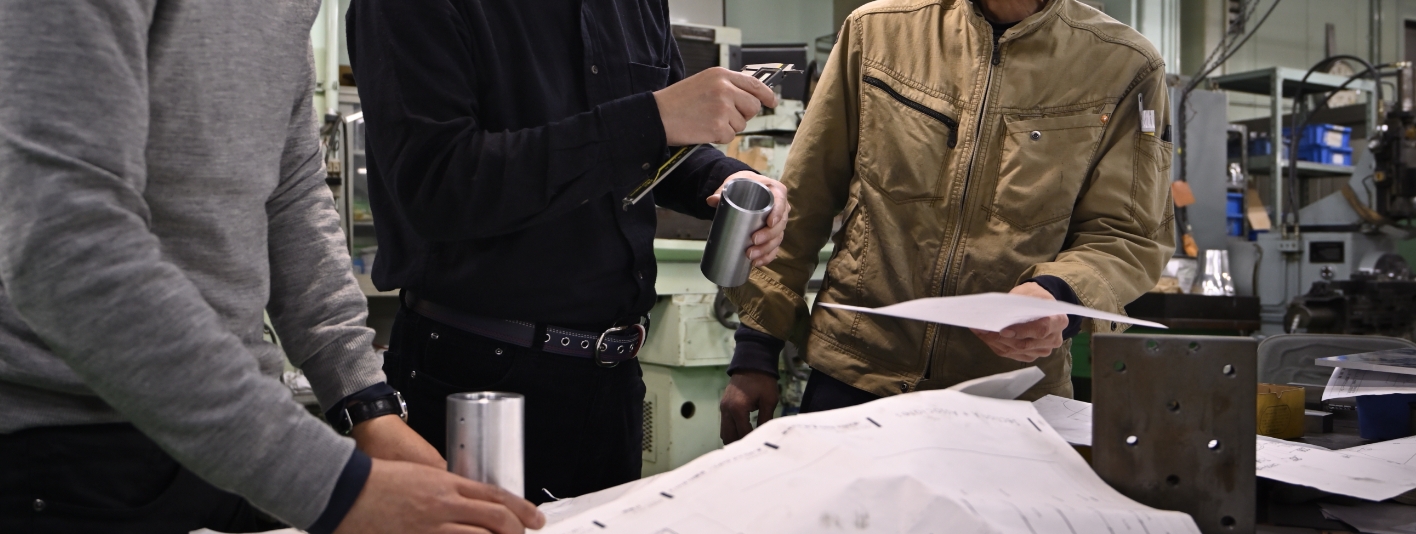
伴走するスクラム型のモノづくり
OEM/ODMで御社の製造部門をアウトソース
「企画」と「販売力」を持つお客様と、「製造スキル」がある当社。
モノづくりのプロがお客様と伴走して“同じチーム”として支えあい、製品を作り上げていくことができる当社では、それを「スクラム型のモノづくり」と呼んでいます。
当社は、「下請け体質からの脱却」をモットーとしており、企業様の製造部署の一貫であると認識しています。両社共にメリットとなれるようなご提案や、きめ細やかに対応できるように心がけています。当社がこれまで培ってきたノウハウや技術・設備は、すべてお客様と共にあります。工場力・提案力・設計力・量産力をはじめ、試作・検証・試組み・製品管理、そして実際にモノに触れる現場プロのフィードバックなど製品化に必要なものは全て揃っています。
さらに東大阪という工場の町ならではの業種の垣根を超えた横繋がり「東大阪ネットワーク」も柔軟に活用。お客様と一丸となって同じゴールを目指し、製造工場としての使命を全うします。
BTO
製造業界をリードする【 Build To Order 】型の受託生産システム
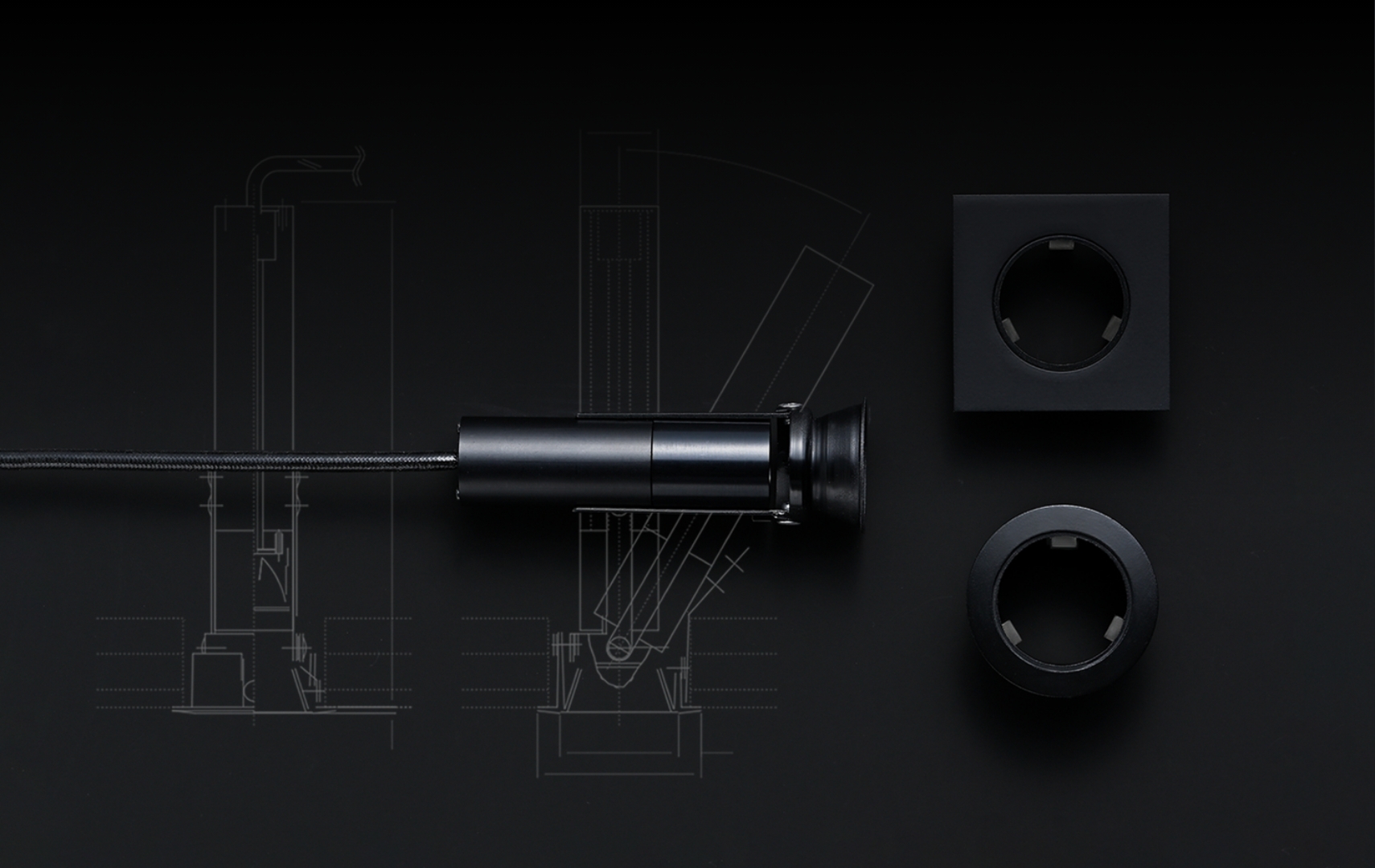
注文=Orderを受けてから
製造=Buildする。
Build To Order
BTO( Build To Order)とは、お客様からのご注文(Order)に応じて製造(Build)する生産方式です。
当社が所有するパーツを流用することで初期投資が抑えられ、かつ、お客様の完成品在庫リスクを回避できます。
投資コストを抑える
BTO型受託生産
盛光SCMのPBパーツ流用し、投資コストを抑えた製品開発を実現
新製品の開発には、長い道のりがあると思っていませんか?
その中でもっとも初期投資が必要なのは「金型投資」です。通常、パーツの量産化までには時間もお金もかかりますが、その部分を当社が所有するパーツを流用すれば、まるっと解決します。
とくに当社が注力する照明器具に関しては、PB照明ブランド「NEEL」で製造した各種類さまざまな照明器具パーツや過去に投資した金型があります。照明器具は、光源・電源・器具本体など各種パーツの組み合わせにより構成されています。お客様はそのパーツを組み合わせて流用し、足りないパーツだけを投資すればよいのです。当社では、ご注文(=Order)に応じて製造(=Build)するBuitd To Order型受託生産方式を取り入れています。
BTO型受託生産の特徴
○ 当社保有のパーツを流用することで初期投資を抑えられる
○ 開発スピードが速い
○ 検証保証取得済み( LEDモジュールの温度検査・器具の配光測定等)
○ 組立~配送までのフルフィルメント体制
板金工場から組立工場までの製造機能を自社で所有する当社では、「試作品や量産最終製品の短納期化」を、在庫ではなく在庫リスク回避を考慮した「受託製造」で実現しています。
市場の流れや変化が激しい今だからこそ初期投資や保有在庫を抑え、スピード力をもった開発及び生産体制をとるべきだと考えています。
BTO型受託生産 | OEM生産 | |
---|---|---|
初期投資コスト | 低い | 高い |
開発スピード | 速い | 通常通り |
パーツの在庫リスク | 低い | 高い |
投資償却期間 | 短い | 通常通り |
製品原価 | 低減 | 通常通り |
ずっと引き継いでいきたい
made in JAPANESE
日本のモノづくりを守り続けるために、
盛光SCMが想うこと
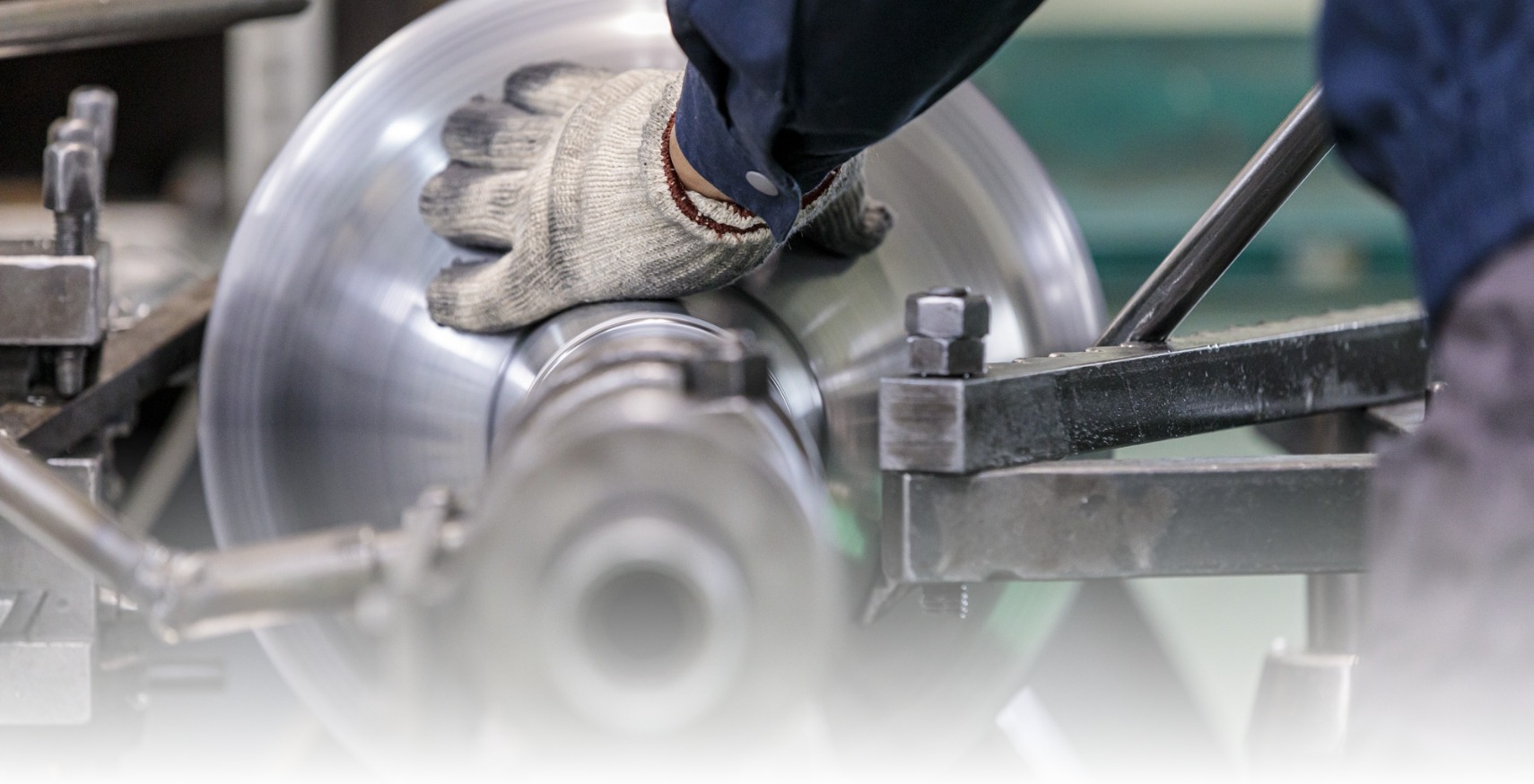
国内生産への
シフトチェンジ
海外と国内のメリットを活かした
生産体制
海外生産と国内生産、どちらも一長一短あります。
ならば、製品・部品の特性やロット数などを鑑みて海外と国内を使い分けることが効率的かつ安定的な調達方法と言えるのではないでしょうか。
製品化するうえで一番のリスク、それは「在庫」です。
海外生産は通常、大量ロットで生産をしなければなりません。
大量ロット → 売れない or 不良発生 → 在庫が残る → 廃棄 の悪循環が発生しやすいのが海外生産。
その最適解が「最終段階を国内生産にシフトチェンジ=在庫リスクの回避」です。
製品・パーツの特性やロット数などを鑑みて、海外と国内の使い分けをすることが効率的かつ安定的な製造方法だと考えます。
つまり、製造スキルをもつ国内工場が海外部品の調達責任と品質保持責任を負い、メーカー側は最終調達先を国内に切り替える。
それが、製品品質の安定化を図り、在庫リスクの低減が可能となるのです。
また、最終製品を made in JAPAN にすることでユーザーからの信頼性もアップするでしょう。
環境試験まで対応している当社なら、製品保証まで請け負うことも可能です。
大量ロットが必要なパーツは海外生産で継続し、それ以外のパーツは国内生産に切り替える。
お客様にとっても国内工場にとっても環境問題にとっても、多大なメリットが生まれます。
国内生産 | 海外生産 | |
---|---|---|
製品原価 | 高 | 低※ただし、海外調達コスト上昇傾向 |
管理コスト | 低 | 高 |
ロット | 小 | 大 |
納期 | 早い | 安定 | 不安定 | カントリーリスクあり |
対応力 | 早い | 安心 | 不安定 | 文化の違い |
品質管理 | 安定 | 不安定 | 文化の違い |
地域貢献 | 〇 | × |